Ultrasint® TPU01
Ultrasint® TPU01 is an elastomer, a flexible material belonging to the thermoplastic polyurethane family, and has been developed for HP’s Multi Jet Fusion 3D printing technology. This material presents a very high elasticity, characterized by an elongation at break of over 260%. Along with this flexibility, Ultrasint® TPU01 is a strong, durable material offering great rebound and shock absorption capabilities.
Thanks to these properties, this high-performance material has much to offer to final part production projects: Ultrasint® TPU01 can indeed be utilized along with lattices to design light sports equipment, footwear, and orthopedic soles, but can also be used for other applications such as car interior component or tool manufacturing.
Other than its performance, Ultrasint® TPU01 combines a great surface quality and a potential for advanced finishings. The raw material is grey and can undergo chemical smoothing to get a shiny black finished look.
Parts printed with Ultrasint® TPU01 should be provided with a 0.8 mm minimum wall thickness.
via GIPHY
Ultrasint® TPU 88A
Ultrasint® TPU 88A is, just like Ultrasint® TPU01, a thermoplastic polyurethane presenting similar fatigue resistance, flexibility, energy return, and shock absorption capabilities. Designed for SLS 3D printing technologies, this elastomer shows a high UV resistance and resilience after deformation.
Unlike its Multi Jet Fusion counterpart, Ultrasint® TPU 88A parts come out white and can be post-processed with chemical smoothing to get a slightly translucent finished look. Parts produced with Ultrasint® TPU 88A should also have a 0.8 mm minimum wall thickness.
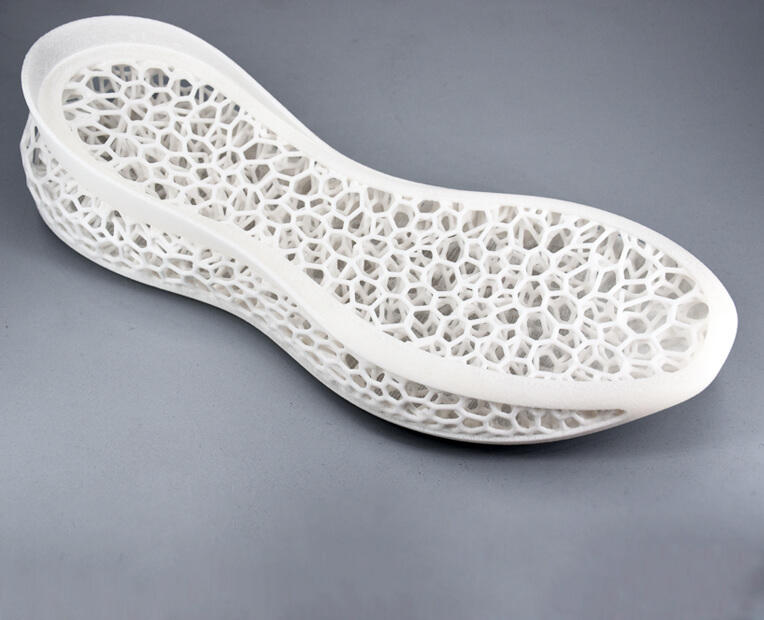
PEBA
What is PEBA material? PEBA is a plastic material, but a little bit different than hard plastic materials we are used to working with in the additive manufacturing industry. Indeed, it is a rubber-like material, it is flexible but also quite resistant, which makes it quite an interesting material. It can totally resist to stress and fatigue. PEBA 2301 is great for both experienced professionals and beginning designers because of its high precision and low cost. Unpolished, the material is white, granular, and somewhat porous.
Elastomeric Polyurethane
Elastomeric Polyurethane, also referred to as EPU, is a high-performance polyurethane elastomer. Developed for CLIP DLS processes, what makes this material stand out is its great elasticity under cyclic tensile, compressive loads, and under wide-ranging temperatures.
The stretchability and durability of EPU make it a perfect fit for applications in which tear and impact resistance are needed. Examples of applications for this resin are gaskets, grommets, cushioning, and flexible watertight seals. This material comes out black, with a rubbery touch, and can be polished in order to get all supports or eventual bumps removed. The minimum wall thickness EPU parts are to be provided with is 1mm with supports or 2.5mm without supports.

Flexible Filament
Using a desktop 3D printer, you could also use a flexible filament in order to manufacture your parts. 3D printing with flexible filaments using the FDM technology could be a solution for you to make some rapid prototyping.