Polyethylene terephthalate (PET) is a semi-crystalline thermoplastic polymer in the polyester family. It is produced through the polymerization of ethylene glycol and terephthalic acid, derived from oil and gas.
Ultrafuse® rPET is our new recycled filament, produced from post-industrial recycled grade PET, making it an excellent alternative to virgin PET.
It is a highly versatile plastic known for its stiffness, strength, flexibility and overall good mechanical properties. Lightweight and resistant to impact, moisture, and solvents, it can be used in a broad range of applications, and is suitable for food contact under the European Plastics Regulation.
One of the world’s most instantly recognizable plastic objects is certainly the plastic water bottle. PET is mainly known as a packaging for water and carbonated drinks, but has been increasingly used as recycled fiber for garments and other objects, due to its great recycling potential and availability.
Considering the vast amount of virgin PET plastic that is produced every day, and the fact that 44% of total waste is generated by plastics, it seemed particularly relevant to try and come up with a solution. PET is a widely popular material for everyday objects; however, it is also an important concern when it comes to plastic waste, handling, and recycling. That is why we are happy to add this recycled PET filament to our materials offer.
This new recycled filament enables us to cut down on 60% of CO2 emissions compared to virgin PET*, while being just as performant.
As you can see below, rPET filament presents a serious environmental advantage over virgin PET filament:
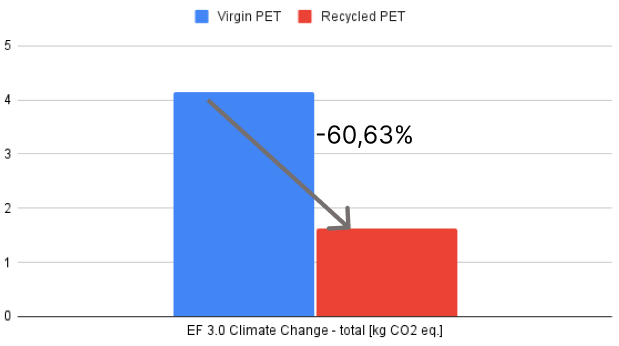
*in a cradle-to-gate life cycle analysis up to the filament production
Source: Forward AM Sustainability Department
Even if this rPET material is easy to 3D print, please keep in mind that specific design guidelines need to be respected, in order to avoid any problem during the additive manufacturing process.
Be sure to check the material design guidelines while creating your 3D file, and before you send it for 3D printing.
If you want to know more about the general properties of rPET filament, you can check our “Technical Specifications” part.