This process has been designed for thermoplastics and can be used along with multiple materials. Now that you know what the benefits of chemical smoothing are let’s talk about how it applies to different plastic materials.
SLS Nylon PA12
This plastic material is used for applications across a wide variety of industries. When it comes to chemical smoothing, this technology is often combined with parts printed in Nylon PA12 such as electronic enclosures, figurines, or objects designed with organic shapes. Indeed, items designed with straight lines are usually homogenous, while parts with curves and round edges tend to display ridges that may need some refinement, hence the usefulness of this finishing option. Going further with its applications, Nylon PA12 is also prized for its bio-compatibility and is a nice fit for medical equipment production. Note that chemical smoothing doesn’t have any bearing on this property, as the technology has been certified for medical uses and as parts processed with it don’t show any cytotoxic effect.
Objects printed with Nylon PA12 come out white and with a granular aspect. Chemical smoothing can be employed to refine the surface and turn it glossy, or, with dying to apply color and smooth the surface.
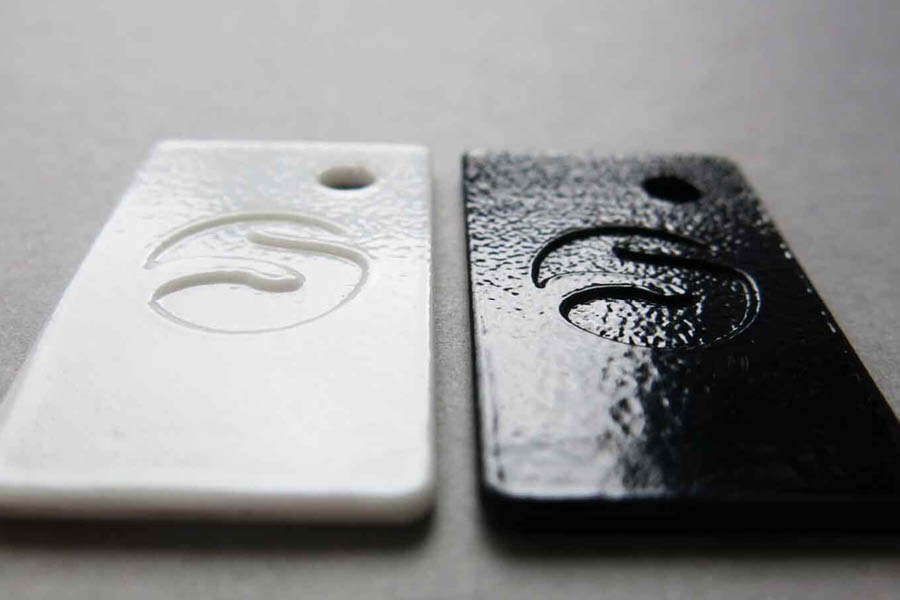
Ultrasint® TPU01
This elastomer is a high-performance material and can be utilized for high flexibility applications in industries such as sports equipment or Automotive.
Ultrasint® TPU01 has been developed for HP’s Jet Fusion technology and is utilized for mechanical part production projects. It can be complemented with chemical smoothing without risk of degrading mechanical properties. Parts processed with this technology are sealed and perform better with fluids, and still benefit from the flexibility and sturdiness of TPU.
Ultrasint® TPU01 comes out grey, and once processed with chemical smoothing, it becomes black with a glossy look. The difference in results before and after the process is drastic, as chemical smoothing significantly improves the surface finish of Ultrasint® TPU01 and completely removes its original granular look.
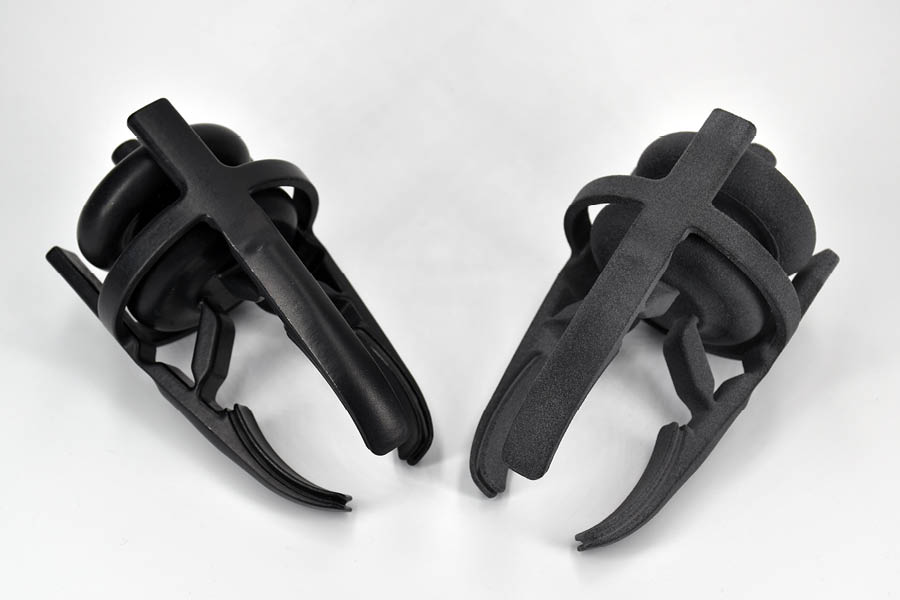
Processed Ultrasint® TPU01 part (right) and raw part (left)
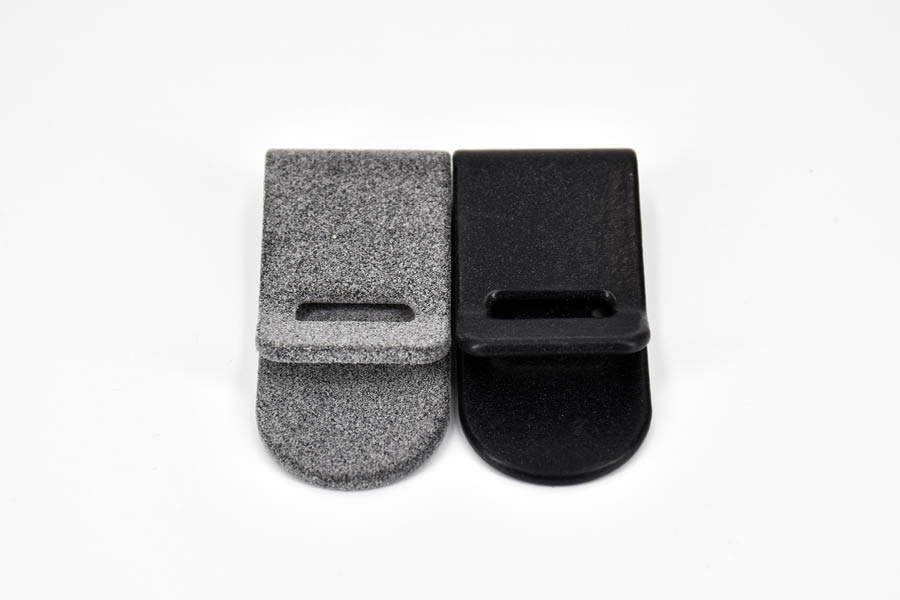
Raw Ultrasint® TPU01 part (left) and processed part (right)