In order to implement additive manufacturing inside a demanding sector, such as the automotive industry, you need to use adapted materials. The mechanical properties you expect from traditional manufacturing are now available with 3D Printing with high-performance materials. Here are the best 3D printing materials to use for automotive applications:
Some plastic materials, such as Polypropylene, are highly used in the automotive industry. Ultrasint® PP nat 01 has a mechanical profile enabling new applications, especially for the automotive industry. For example, Polypropylene can be used to 3D print interior components, dashboard parts, airflow, or adapted fluid systems.
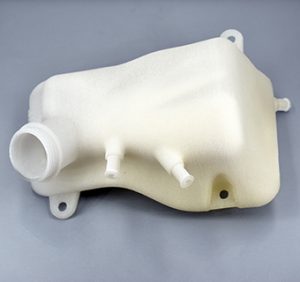
Additive manufacturing allows for other possibilities with materials offering thermal resistance such as Ultrasint® PA6 FR an advanced engineering polymer powder containing a flame-retardant (FR) additive. This material combines excellent mechanical and thermal performance with flammability requirements; it is especially suited for applications in the electronics and transportation sector.
Ultrasint® PA6 MF highly resistant and perfect to create functional parts for engine bay parts and many other parts in the transportation sector. PA6 is strong enough to hold the whole engine assembly and handle all heat, vibration, and static loads. Thanks to 3D printing and the media tightness of this PA6 MF material, you can create made-to-measure chemical resistant parts such as 3D printed reservoirs.

Are you looking for a resistant and flexible material? With impressive properties such as high rebound, low compression set, and good fatigue behavior, TPU is ideal for applications requiring shock absorption, friction, or flexibility!
Ultrasint® TPU 88A or Ultrasint® TPU 01 can both be used in the automotive industry to create car interior components, for example. With a Shore A 88, air filter covers, bellows gimbal, or any flexible and resistant parts needed in the automotive industry can be 3D printed using TPU.
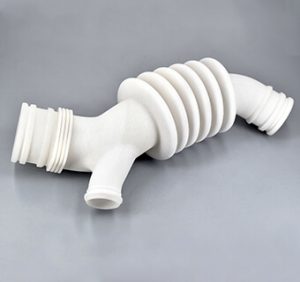
It is also possible to use more sustainability into your manufacturing process using bio-derived materials. 3D printable Nylon PA11 is based on 100% renewable biomass sources. The Castor seed is extracted from the castor plant to make oil. The oil is then converted into the monomer (11-aminoundecanoic acid), which is finally polymerized into Polyamide 11. Here are some options adapted to the creation of automotive parts:
- Ultrasint® PA11 & MJF PA11: These PA11 are bio-based materials, perfect to create durable parts. Living-hinges, parts with high impact resistance, these Nylon PA11 materials are offering great opportunities.
- Ultrasint® PA11 CF is a 3D printing material reinforced with carbon fibers, providing advanced mechanical performance for your parts when strength and rigidity are needed. Does your project require a high strength-to-weight ratio, high impact resistance? Ultrasint® PA11 CF might be the perfect solution.
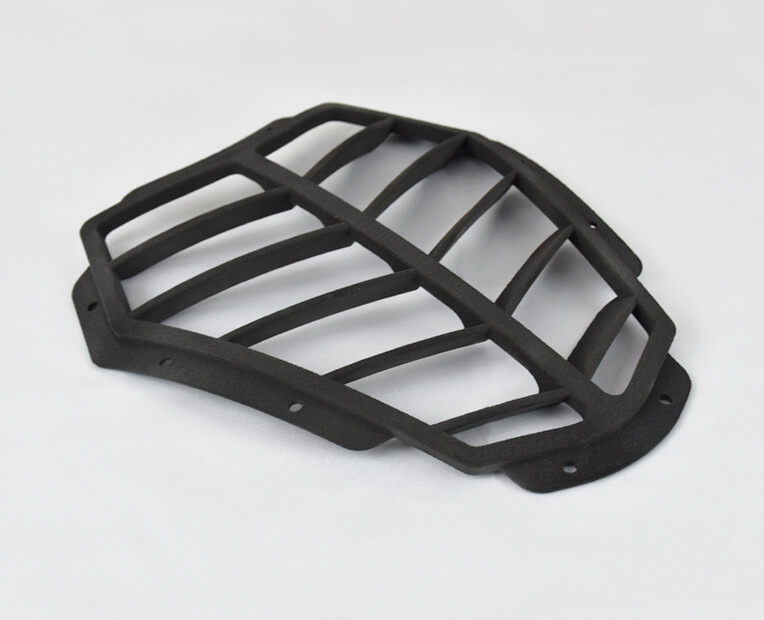