Home » 3D Printing Materials » SLS technology » Ultrasint® PP nat 01
Ultrasint® PP nat 01
3D printing material
Ultrasint® PP has a lot of valuable properties, boasts excellent plasticity, higher elongation, durability, and low moisture absorption. Its high rigidity makes it especially well-suited for technical applications and durable 3D printed polypropylene parts.
Ultrasint® PP nat 01 Material Guide
What is PP nat 01?
Polypropylene or PP is a semi-crystalline thermoplastic polyolefin. This advanced material powder is popular for a wide range of innovative applications. Indeed, Polypropylene is part of standard plastics and is the most used polymer; which is now useable with additive manufacturing!
3D printing PP offers the possibility to make the most of the well-known characteristics of this plastic: excellent chemical resistance, media tightness, and ductility. The rigidity of this PP plastic material makes it really well suited for technical applications and durable 3D printed parts. This white and translucent material has great technical features, especially useful to improve your production process.
This PP nat 01 material is 3D printed using Selective Laser Sintering technology. Please keep in mind that you will have to respect specific design guidelines to avoid any problem during the additive manufacturing process. Be sure to check the material design guidelines while creating your 3D file and before you send it for 3D printing.
What are the possible applications of polypropylene?
Are you looking for a 3D printing material offering strength, ductility and stiffness to manufacture your end-use parts? Our PP 3D printing material printed using SLS technology has a mechanical profile enabling new applications, especially for the automotive industry and the consumer goods market. For example, Polypropylene can be used to 3D print interior components, dashboard parts, airflow, or fluid systems for the automotive sector. PP 3D printing material is perfect for industrial uses, from pipes to machinery.
The formula of PP nat 01 has excellent plasticity, a higher elongation, and low moisture absorption. Tubes, tools, jigs, and fixtures can be easily 3D printed using this PP material.
PP can become an alternative to Nylon PA12 if you want a resistant material, perfectly suited for production!
- Chemical Resistant
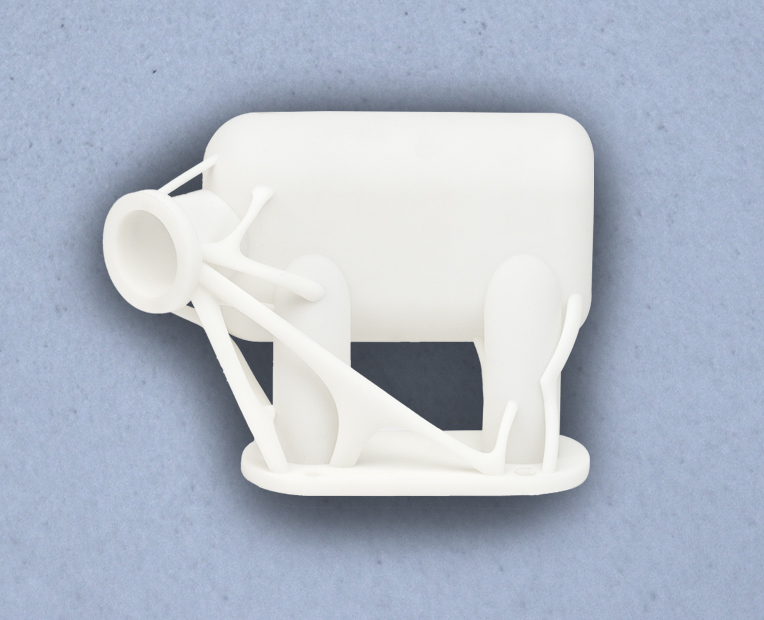
Thanks to its high chemical resistance, it is possible to use it to create reservoirs for nearly all kinds of media and chemicals, or solvent resistant packagings.
Strong and Lightweight
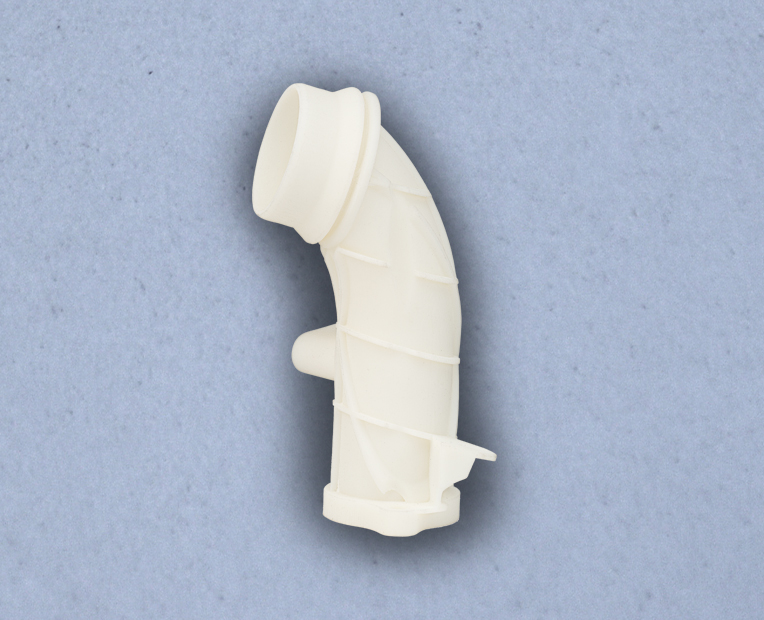
Density: 0.890
Manufacturing strong and lightweight is important for various sectors, such as the automotive and consumer goods fields. PP is resistant to strong impacts.
Airtight and Watertight

Polypropylene material is perfect to create fluid reservoirs. Using additive manufacturing to create reservoirs or packagings will allow to produce parts with intricate shapes, perfectly adapted to your space constraints.
Pricing
The printing price of your design is calculated automatically the moment it is uploaded. As you modify your object (changing material, finishing, size, using batch control or hollowing feature, etc.) you will note that the price changes automatically. The pricing is based on a series of factors, including total volume, object size, and bounding box – to name a few.
The estimated shipping time is also calculated automatically as the object is uploaded and each time you make a modification on it. Delivery time should be added to processing time.
For more information, check our pricing page.
How does SLS 3D printing technology work?
Sculpteo uses a layer by layer process called Selective Laser Sintering (SLS) to manufacture PP parts.
The Selective Laser Sintering technology uses a highly specific laser that sinters thin layers of powder together one layer at a time. After each round of lasering, the printing bed is lowered and another layer of powder is evenly swept across the top for another round of sintering. This 3D printing process continues until the part is fully printed according to the 3D file.
Maximum size | 260 x 260 x 300mm |
The maximum size of your models are limited by the physical size of our 3D printers – nothing can be printed larger than the printer bed. |
Due to the printing process, your objects will have upskin and downskin. Upskin is a little concave, whereas downskin will show slight convex. Upskin will appear on the top of your object, downskin at the bottom. This is important to consider when you set the orientation of your 3D model. If the upskin and downskin will affect your design, set the orientation beforehand and we will honor it, if you are not sure, our technicians will choose the best one. |
Standard layer thickness | 120µm |
Accuracy | ± 0.3% (minimum of ± 0.3 mm) |
Minimum wall thickness | 1mm |
Stemmed elements with support | 1mm |
Stemmed elements without support | 1.2mm |
Minimum height and width details | Embossed : 0.7 mm
|
Ratio Depth / width | 1/1 |
Enclosed parts ? | Yes |
Interlocking parts ? | Yes |
Our material has the ability to print the most complex designs of our materials . An example of a complex design is a volume enclosed within another volume, like a chain or a ball joint connection. Our printers have the ability to print a fully interlocked chain, with no support structures to remove. |
Minimum spacing between fixed walls | 0.7 mm |
Minimum clearance between parts | 0.7 mm |
For a successful 3D print a minimum clearance between objects is required to allow excess material to be sand blown out. If this space is not left within the design, the object will be a solid. This is particularly important for articulated objects – as the space left between the walls will define the object’s ability to move.
Clearance should be at least 0.5 mm, however that is the minimum for small objects. Larger objects require more space between their parts. This is due to the HP printing process. Our printer beds are heated during the process, and larger objects are heated for longer periods. A small space between large objects runs the risk of melting together as it remains under heat for a long period of time. In some other cases, holes should be added to allow us to drain for the excess powder material within the clearance.
Hollowing ? | Yes: 5mm |
Our online hollowing optimization tool has the ability to greatly reduce the price and the weight of a print by reducing the amount of material used. Using the tool requires adding two holes to your model, which will serve as the drain for the excess powder material within the object. The minimum size of these holes is determined by our website. Otherwise, it is possible to hollow your object manually in your 3D modeling software. |
Ready to 3D print with PP?
With Sculpteo’s online 3D printing service you’re just a few clicks away from professional 3D printing. Your 3D model is printed with the highest quality and delivered straight to your door.
Get started now!